Co je to koroze CO₂ a jak je definována?
Různé / / August 07, 2022
Koroze CO2 je korozivní jev produkovaný přítomností plynného CO2, tj se rozpouští ve vodné fázi a může vyvolat generalizovanou nebo lokalizovanou korozi, hlavně v ocelích na uhlík.






Chemický inženýr
Vzhledem k tomu, že ze všech poruch, ke kterým dochází při provozu zařízení a potrubí, která přepravují zemní plyn resp oleje, 33 % z nich je způsobeno korozními jevy, tento typ koroze hraje roli základní. Je známo, že 28 % z nich je způsobeno „sladkou“ korozí CO2, zatímco 18 % poruch pochází z „kyselé“ koroze H2S.
Vnitřní koroze (na vnitřním povrchu) je obecně způsobena přítomností vody ve spojení s jdeš ven, oxid uhličitý (CO2) a sirovodík (H2S). Proto je oxid uhličitý korozivní rozpuštěný plyn, jehož rozpustnost závisí na faktory jako je tlak a teplota provozu. Pokud se CO2 dostane do kontaktu s vodou v chladicím systému Výrobato bude ovlivněno, protože při parciálních tlacích tak nízkých, jako je 3 psi, může dojít k ředidlu.
Když CO2 přítomný v přepravované kapalině reaguje s vodou rozpuštěním, vytváří kyselinu uhličitou, která interaguje se železem (hlavní složkou uhlíkové oceli), což vede ke globální reakci, která generuje vodík a ionty. Kromě toho může CO2 reagovat se železem za vzniku uhličitanu železnatého (FeCO
3).V přítomnosti kyseliny uhličité železo reaguje za vzniku uvedeného uhličitanu a sráží se. Proto je tento typ koroze snadno identifikovatelný na základě jeho morfologie poškození a nalezených korozivních produktů, jako jsou uhličitany železa a oxidy železa. Zapojené reakce jsou následující:
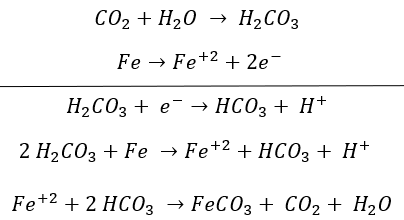
Jak jsme uvedli dříve, rozpustnost oxidu uhličitého hraje zásadní roli, protože jak se zvyšuje, ve vodné fázi bude rozpuštěno více plynu. Tato rozpustnost, stejně jako u většiny plyny, roste s rostoucím celkovým tlakem a klesající teplotou. Závažnost poškození, ke kterému dochází, tedy silně závisí na těchto faktorech, protože se zvyšuje koncentrace CO2 ve vodné fázi. Když se vyrábí kyselina uhličitá, pH řešení výsledný je menší, to je také faktor, který je třeba vzít v úvahu při hodnocení jeho korozní rychlosti a vzniklého poškození.
API 571 určuje, že materiály nejvíce postižené tímto typem koroze jsou: uhlíkové oceli a nízkolegované oceli. Zatímco zvýšení obsahu chrómu ve složení oceli větší než 12 %, typ 410 SS, dosahuje větší vytrvalost. Stejně tak je austenitická nerezová ocel řady 300 považována za odolnou vůči korozi CO2.
Koroze CO2 nebo sladká koroze se projevuje různými způsoby v závislosti na jednotce a zařízení, se kterým pracuje. Podobně se tato morfologie poškození může lišit v závislosti na interakce s jinými korozivními činidly v prostředí, jako je sirovodík, kyslík nebo dokonce chloridy, které urychlují korozní reakce. Je známo, že přítomnost chloridových iontů snižuje stabilitu ochranné vrstvy. tvořený jak vysráženým uhličitanem (FeCO3), tak i magnetitem (oxid železa, Fe304). Proto se zvyšující se koncentrací chloridů bude pravděpodobnější korozivní jev.
Obecně lze pozorovat generalizovaný nebo lokalizovaný útok. Když je toto poškození lokalizováno v určitých oblastech, které jsou nejvíce postiženy, lze identifikovat důlkovou korozi (v oblastech proudění těsné nebo polotěsné), útoky typu „stol“ (plochého typu) nebo dokonce „prohlubně“ v oblastech s vysokou rychlostí tok. To znamená, že morfologie je také závislá na mnoha parametrech, jako jsou ty již zmíněné, a dokonce na přítomnosti nebo nepřítomnosti částicového materiálu.
Aby se zabránilo tomuto typu mírné koroze, běžně se používají inhibitory koroze, které tvoří jakýsi film nebo „film“. povrchový chránič, který funguje jako „bariéra“ a dokonce i další typy inhibitorů, které mohou neutralizovat kyselost produkovanou plynem rozpuštěný. Nakonec se také rozhoduje o použití materiálů, které jsou vůči tomuto typu koroze odolnější.
Reference
Asrar, N., MacKay, B., Birketveit, Ø., Stipanicev, M., Jackson, J., Jenkins, A.,... & Vittonato, J. (2016). Koroze: Nejdelší boj. Oilfield Review, 28(2), 36-51.American Petroleum Institute (Wash.). (2011). Mechanismy poškození ovlivňující pevná zařízení v rafinérském průmyslu: Doporučený postup API 571.