Destillasjonstårn/kolonne definisjon
Pålitelighet Elektrisk Motstand / / April 02, 2023

Kjemisk ingeniør
Destillasjonstårn eller kolonner er trykkbeholdere hvor separasjonen av de ulike komponentene som utgjør tilførselsstrømmen skjer. Driftsprinsippet er basert på forskjellen mellom fordampningstemperaturene til hvert av stoffene og deres flyktighet.
Teoretisk fundament
Som all destillasjon er essensen av prosessen basert på ordningen:
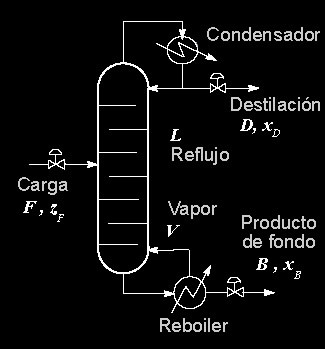
Et destillasjonstårn har en varmekilde i det nedre området, for eksempel Gjenkoker, som genererer det, takket være levering av kalori energi, går en del av komponentene (en eller flere) over i dampfasen. Når de stiger opp gjennom kolonnen, vil de møte den synkende væsken, for Derfor, når den når toppen av kolonnen, mates dampstrømmen mest flyktige I mellomtiden ble de tyngre komponentene dratt av væsken som falt ned i en motstrøm. Det er derfor væskestrømmer sies å være på boblepunktet, mens dampstrømmer sies å være på duggpunktet.
Når disse strømmene utveksles energi, de utveksler masse samtidig og det skjer på hvert trinn, det vil si på hver plate (det kan også være en fylling) symbolisert som en indre horisontal linje i tårnet.
Når dampfraksjonen når toppen av tårnet, går den til en kondensator, hvor den oppnås det destillerte produktet og hvor en del av den strømmen, kjent som refluks, kommer inn igjen i tårn.
Det må tas i betraktning at i det forrige bildet er en destillasjon av binær type tegnet, det vil si bare to komponenter i strømstrøm De skilles, trekker ut en fra toppen og den andre fra bunnen. Imidlertid er det destillasjoner av flere komponenter, hvor det i hvert trinn av tårnet er mulig å skille en annen komponent.
applikasjoner
Bransjene som bruker destillasjonstårn er mange, og avhengig av bruken vil derfor være diameteren og lengden, produksjonsmaterialet og dets type plate eller fyll. For eksempel er et destillasjonstårn raffineriets hjerte av råolje i verden. Når oljen kommer til et renseanlegg, gjennomgår den først en avsaltningsprosess og deretter høytrykksovner. temperatur. Deretter introduseres den til selve tårnet, hvor de mer flyktige komponentene stiger gjennom stadiene og av høyere koketemperatur faller mot bunnen av tårnet og kondensatene på toppen samles i bøtter.
For å opprettholde temperaturen i tårnet er det ulike mekanismer, spesielt her resirkuleres vanligvis dieselolje og parafin (komponenter av den opprinnelige blandingen), før de kommer inn igjen, avkjøles de i en varmeveksler. varme. Mens "tilbakeløpshodet" på toppen holder riktig temperatur på toppen.
For å forstå den betydelige størrelsen på disse tårnene, mellom 60 m og 80 m i lengde og 6 m i diameter, må vi forstå viktigheten av dette i prosessen. Fra den opprinnelige blandingen er det mulig å skille tung dieselolje (ved 340 °C), lett dieselolje (ved 280 °C), parafin (ved 210 °C) og nafta (ved 180 °C), får derfra den omfattende lengden som er nødvendig for å dekke alle fraksjoneringsstadiene i blande. I sin tur oppnås den tyngste komponenten i bunnen av tårnet: fyringsolje.
I fraksjoneringsanlegg brukes de også til å søte gassen, for eksempel i aminkontaktortårn, hentes den fra toppen søtgassen, mens i bunnen aminstrømmen med sur gassinnhold, strøm som sendes til et annet tårn for sin regenerering. De brukes også i andre bransjer, for eksempel i produksjon av organiske forbindelser og av polymerer.
Som forventet finnes det også en rekke produksjonsmaterialer, fra glass for destillasjonskolonner til skala laboratorie- eller pilotskala til store tårn laget av karbonstål eller lavlegert stål. På den annen side, hvis det er kjent at de vil fungere med en svært korrosiv væske som gasser med CO2- og H2S-innhold, er de vanligvis laget av rustfritt stål eller andre motstandsdyktige legeringer. Det er også vanlig å finne tårn med forskjellige materialer avhengig av seksjonene, siden for eksempel den kritiske sonen til kondensasjon For sure gasser kan den øvre delen være laget av rustfritt stål eller ha kledning mens den nedre delen kan være laget av karbonstål.
Designet er basert på tjenesten din og må oppfylle strenge standarder for kvalitet, sikkerhet og produksjon som gir designstandarder, slik som ASME VIII.