Визначення дистиляційної вежі/колонки
Надійність Електричний опір / / April 02, 2023

Інженер-хімік
Дистиляційні башти або колони є посудинами під тиском, де відбувається розділення різних компонентів, що утворюють потік сировини. Принцип дії заснований на різниці між температурами випаровування кожної з речовин і їх леткістю.
Теоретичні основи
Як і будь-яка дистиляція, суть процесу заснована на схема:
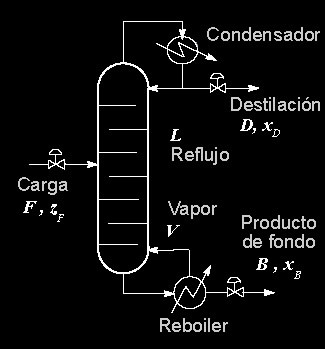
Дистиляційна вежа має джерело тепла в нижній частині, наприклад Ребойлер, який створює це завдяки доставці калорійність енергії, частина компонентів (один або декілька) переходить у парову фазу. Коли вони піднімаються крізь колону, вони зустрінуть низхідну рідину, наприклад Тому, коли він досягає верхньої частини колони, потік пари подається найбільше летючий Водночас важчі компоненти захоплювалися рідиною, яка спускалася протитечією. Ось чому кажуть, що потоки рідини знаходяться в точці кипіння, а потоки пари – у точці роси.
Коли ці струми обмінюються енергії, вони одночасно обмінюються масою, і це відбувається на кожній стадії, тобто на кожній пластині (вона також може бути начинкою), яка символізується як внутрішня горизонтальна лінія у вежі.
Коли фракція пари досягає верхньої частини башти, вона надходить до конденсатора, де отримує дистильований продукт і де частина цього потоку, відома як рефлюкс, знову потрапляє вежа.
Слід взяти до уваги, що на попередньому зображенні зображено бінарний тип дистиляції, тобто тільки два компоненти в силовий струм Їх роз’єднують, витягуючи одну зверху, іншу знизу. Однак існує дистиляція кількох компонентів, де на кожній стадії башти можна відокремити інший компонент.
Додатки
Існує багато галузей промисловості, які використовують дистиляційні башти, і, отже, залежно від їх використання будуть діаметр і довжина, виробничий матеріал і тип пластини або начинки. Наприклад, дистиляційна башта НПЗ серце сирої нафти у світі. Коли нафта надходить на очисні споруди, вона спочатку проходить процес опріснення, а потім – печі високого тиску. температура. Потім його вводять до самої вежі, де більш летючі компоненти піднімаються через ступені та з більш високою температурою кипіння падають у нижню частину башти, а конденсат у верхній частині збирається у відра.
Для підтримки температури в башті існують різні механізми, зокрема тут зазвичай переробляють дизельне паливо і гасу (компонентів вихідної суміші), перед повторним надходженням їх охолоджують в теплообміннику. тепло. У той час як у верхній частині «рефлюксна головка» підтримує правильну температуру у верхній частині.
Щоб зрозуміти значний розмір цих веж, від 60 до 80 метрів у довжину та 6 метрів у діаметрі, ми повинні зрозуміти важливість цього в процесі. З вихідної суміші можна виділити важке дизельне паливо (при 340 °C), легке дизельне паливо (при 280 °C), гас (при 210 °C) і нафти (при 180 °C), звідти виходить велика довжина, необхідна для покриття всіх стадій фракціонування змішувати. У свою чергу, найважчий компонент виходить на дні вежі: мазут.
На фракціонуючих установках вони також використовуються для підсолоджування газу, наприклад, в амінних контактних вежах його отримують з верхнього солодкий газ, тоді як у нижній частині амінний струм із вмістом кислого газу, струм, який направляється в іншу вежу для його регенерація. Вони також використовуються в інших галузях промисловості, наприклад у виробництві органічні сполуки і з полімери.
Як і очікувалося, також існує різноманітність виробничих матеріалів, від скла для дистиляційних колон до масштаб лабораторних або пілотних масштабів до великих веж з вуглецевої або низьколегованої сталі. З іншого боку, якщо відомо, що вони працюватимуть із висококорозійною рідиною, такою як гази з вмістом CO2 і H2S, вони зазвичай виготовляються з нержавіючої сталі або інших стійких сплавів. Також часто зустрічаються вежі з різних матеріалів залежно від секцій, оскільки, наприклад, критична зона конденсація Для кислих газів верхня секція може бути виготовлена з нержавіючої сталі або мати оболонку, тоді як нижня секція може бути виготовлена з вуглецевої сталі.
Його дизайн створено на основі ваших послуг і має відповідати суворим стандартам якість, безпеки і виробництво, яке забезпечує стандарти проектування, такі як ASME VIII.